Project setup with WebHMI
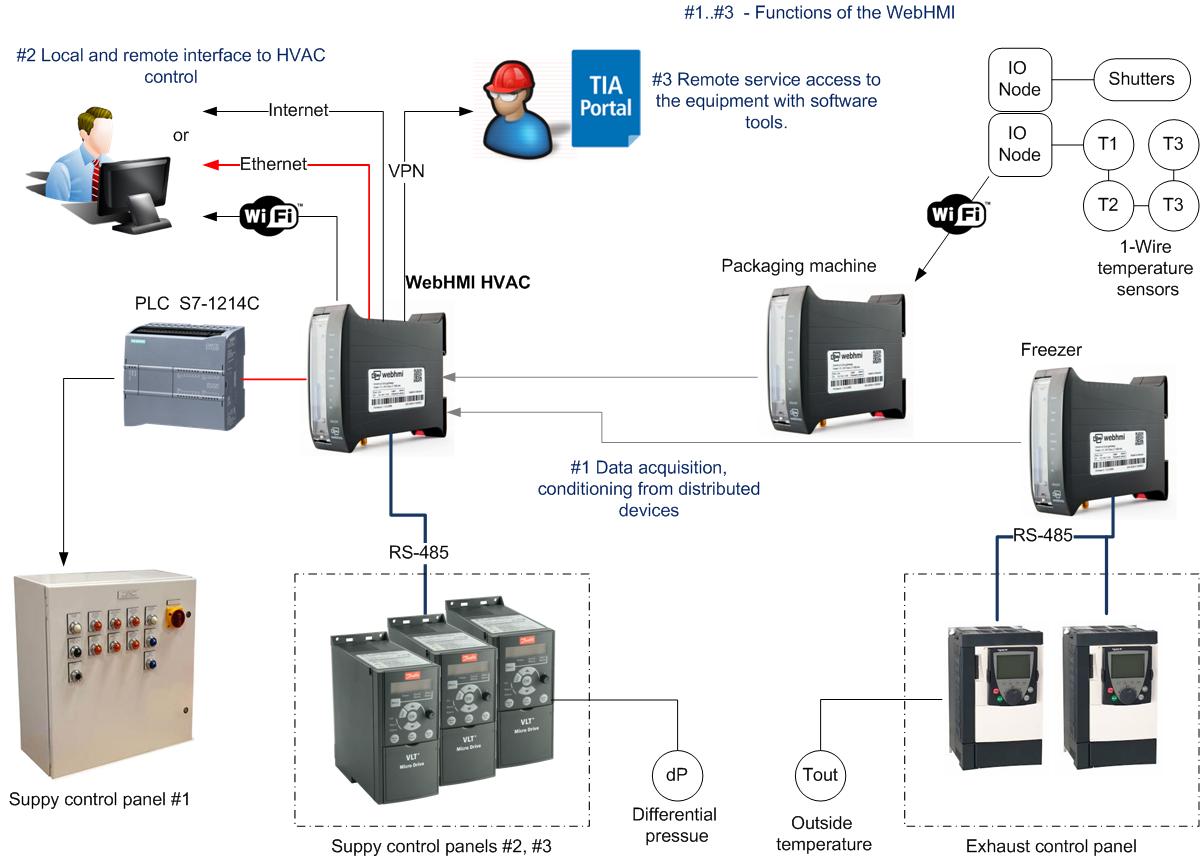
The preliminary design showed that solving the task in “classical way” – feeding all required physical sensors to the PLC (directly or via remote I/O) would become a very costly part of the future project:
- Extra analog sensors (5 temperatures and diff. pressure) with analog speed setpoint signals for variable frequency drives. (8 pcs.)
- Laying cables also was complicate task, because signals from different units had to be laid separately, through the premise for the long distances. Besides, some signal cables could be laid only on girders under the roof with height of 12 meters, and this would be risky part of mounting. Taking into consideration intensive work schedule with 3 shifts, this seemed really difficult task.
- Frequency converters had RS-485 interface and could communicate with PLC over Modbus, but S7-1200 had no serial port, so extra serial communication module was necessary with complicate programming in PLC for serial exchange.
- The HMI able to work with S7-1200 was Siemens KTP, which would cost 3-4 times as much as PLC cost.
So these difficulties made the commercial benefit of the project very low and drove us up to optimizing system structure. The keys to a new, more rational structure were the following:
- There were several WebHMI installed (freezer monitoring, batching system, packing machine monitoring) close to frequency converter control panels and places of possible sensors mounting. These WebHMIs could be used as gateways for sending signals to the new system and so minimizing cable and mounting cost.
- One WebHMI as a communication controller, gateway and operator interface for the PLC.
- There were few free analog inputs on each frequency converters, which can be used for analog sensors.
- Using cheap 1-wire temperature sensors together with IO-Node wireless remote I/O module, which were connected to nearest WebHMI Wi-Fi network (path to a central WebHMI was set up with routes in network settings).
After considering the possibilities that WebHMI would provide in this project: configuration instead of programming the data collection process, the gateway function, visualization and management tools, operator access from different places (internet as well), user scripts, automatic notification via SMS, work in VPN networks and simple organization of remote service access to the system (the possibility of remote work not only with the WebHMI project, but also with the devices behind it – PLC, frequency drive.), – it was clear that WebHMI had not better alternative.
Screenshot of the operator interface
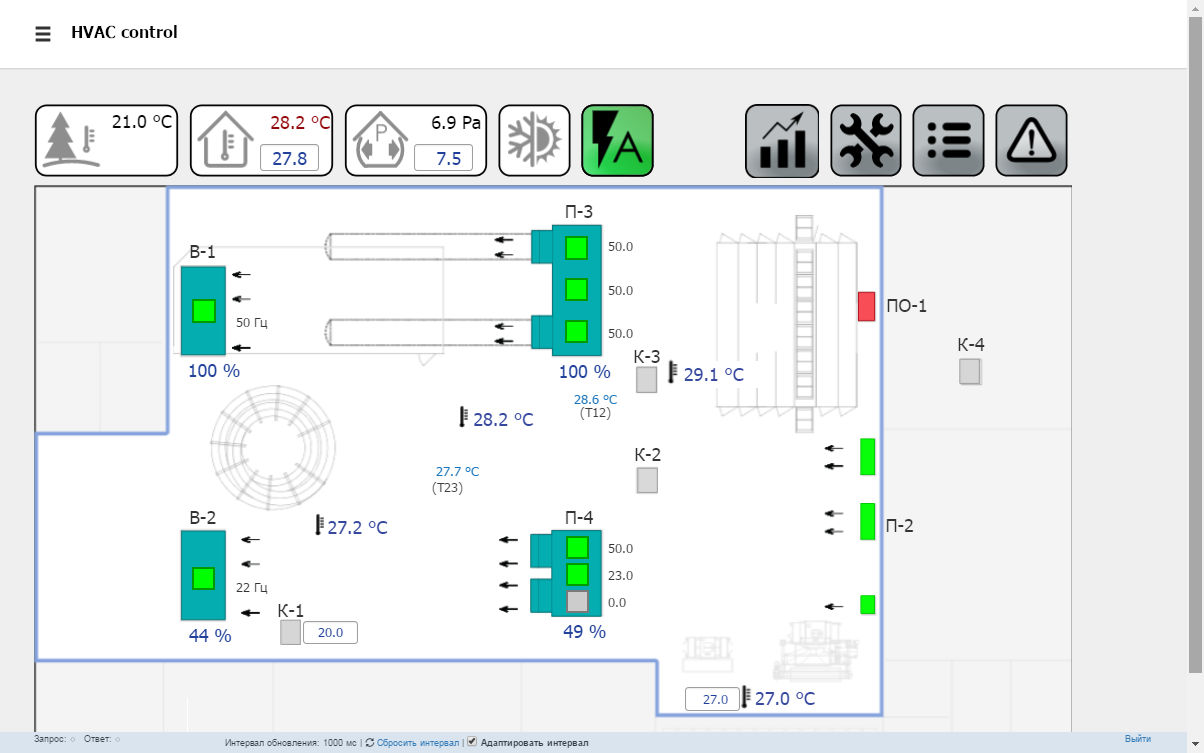
Advantages
- Substantial economy on cables and mounting – minimum length of cables were needed just to wire interface cable to the nearest WebHMI or Wi-Fi network connection w/o any cables.
- Simple PLC program. The central WebHMI polled and conditioned all the signals from different sub-systems and formed one datablock in PLC memory.
- Simple remote control function implementation (manual distant control) – in this mode due to a gateway feature of the WebHMI all operator commands and setpoints from interface screens were just sent to destination remote device, w/o involving PLC. On switching into “auto” mode remote control elements hid using “visibility bit”.
- No need for local HMI operator panel – WebHMI web interface allows accessing the HVAC system from any working place via LAN or event internet.
- With remote service access feature, the commission time in the field was minimized. Most work on interface developing and programming were done remotely from office.
- As a result of par. 1..5, the project was finished within short time and with low expenses. And we were chosen as a winner for the contract among the system integrators dedicated in HVAC.
- The graph and trend in WebHMI allowed to analyze system operation (PID loops for the pressure and temperature control) и make “fine-tune” of the control algorithms.